工件坐标系是编程人员在编程时使用的,由编程人员以工件图纸上的某一固定点为原点所建立的坐标系,编程尺寸都按工件坐标系中的尺寸确定。为保证编程与机床加工的一致性,工件坐标系也应该是右手笛卡儿坐标系,而且工件装夹到机床上时,应使工件坐标系与机床坐标系的坐标轴方向保持一致。
工件坐标系的原点称为工件原点或编程原点。工件原点在工件上的位置可以任意选择,为了有利于编程,工件原点最好选在工件图样的基准上或工件的对称中心上,例如回转体零件的端面中心、非回转体零件的角边、对称图形的中心等。
在数控车床上加工零件时,工件原点一般设在主轴中心线与工件右端面或左端面的交点处如图3-4(a)所示;在数控铣床上加工零件时,工件原点一般设在工件的某个角上或对称中心上,如下图所示。
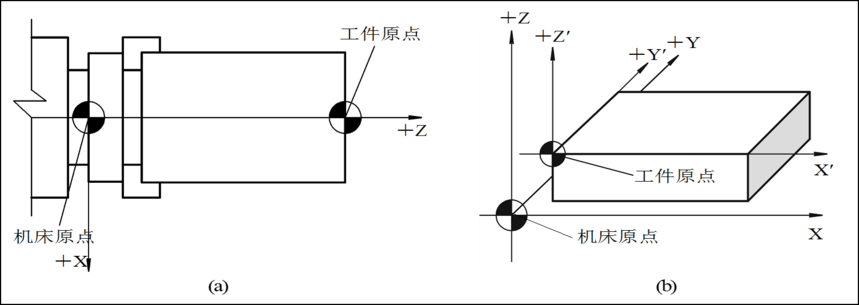
工件原点设置
(a) 数控车床;(b) 数控铣床
工件坐标系和机床坐标系的关系
编程时,尺寸都按工件坐标系中的尺寸确定,不必考虑工件在机床上的安装位置和安装精度,但在加工时需要确定机床坐标系、工件坐标系、刀具起点三者的位置才能加工。工件装夹在机床上后,可通过对刀确定工件在机床上的位置。
所谓对刀,就是确定工件坐标系与机床坐标系的相互位置关系。在加工时,工件随夹具在机床上安装后,测量工件原点与机床原点之间的距离,这个距离称为工件原点偏置,如下图所示。在用绝对坐标编程时,该偏置值可以预存到数控装置中,在加工时工件原点偏置值可以自动加到机床坐标系上,使数控系统可按机床坐标系确定加工时的坐标值。
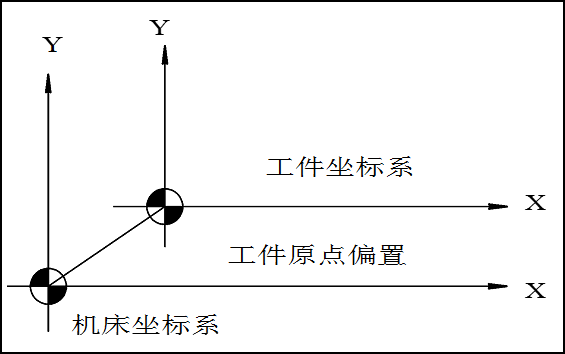
机床坐标系与工件坐标系
对刀过程一般从各坐标方向分别进行,可理解为通过找正刀具与一个在工件坐标系中有确定位置的点(即对刀点)来实现。对刀点可以设在工件、夹具或机床上,但必须与工件的定位基准(相当于工件坐标系)有已知的准确关系,这样才能确定工件坐标系与机床坐标系的关系。选择对刀点的原则是:便于确定工件坐标系与机床坐标系的相互位置,容易找正,加工过程中便于检查,引起的加工误差小。当对刀精度要求较高时,对刀点应尽量选在零件的设计基准或工艺基准上。
对刀时直接或间接地使对刀点与刀位点重合。所谓刀位点,是指编制数控加工程序时用以确定刀具位置的基准点。对于平头立铣刀、面铣刀类刀具,刀位点一般取为刀具轴线与刀具底端面的交点;对球头铣刀,刀位点为球心;对于车刀、镗刀类刀具,刀位点为刀尖;钻头取为钻尖等,如下图(a)~(d)所示。刀具起始运动的刀位点称为起刀点。
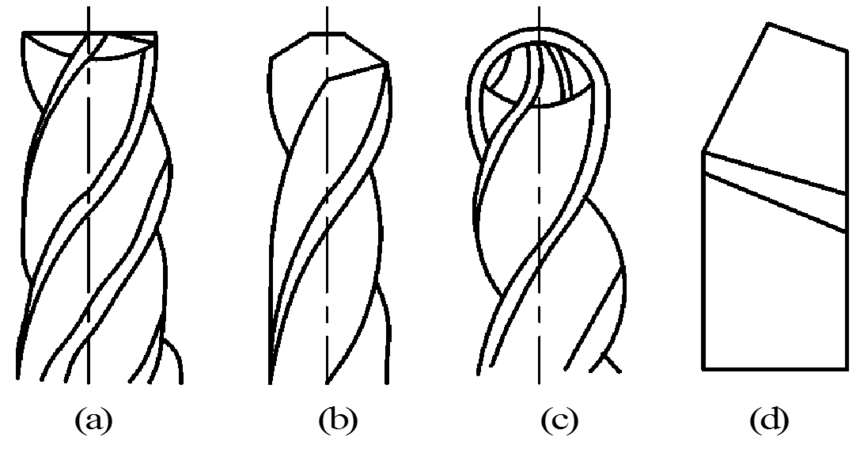
刀位点
(a) 平头铣刀;(b) 钻头;(c) 球头铣刀;(d) 车刀、镗刀
数控系统从对刀点开始控制刀位点运动,并由刀具切削部分加工出要求的零件轮廓,如用球头刀加工三坐标立体型面的零件时,数控系统控制球头刀球心轨迹,而由外圆切削刃加工出零件轮廓。
对数控车床、加工中心等数控机床,如加工过程中要换刀,在编程时应考虑选择合适的换刀位置,为了防止换刀时刀具碰伤工件,换刀点必须设在零件的外部。